in Space
1
st
The first additively manufactured RF amplifier launched into space in March 2021
of Potential Applications
100
s
New horizons for additive processes are now emerging in autonomous flight systems, drones, mini-satellites and more
to Proof of Concept
7
Hours
Generate 3D printed electronic circuit board prototypes and micro parts within hours without reliance on outside vendors
Reinvent Electronics in Your Lab
Groundbreaking technology that gives researchers the freedom to instantly create
Nano Dimension’s DragonFly prints fully functional 3D electronic circuitry in-house.
Researchers can also explore free-form printing of metals and dielectric polymers for entirely new applications.
Unprecedented Form Factors
Multiply layers and freely form connections inside 3D electronic devices
High
Performance
Fabricate embedded antennas, coils and other high-performance passive components
Shortened
Development
Cycles
Immediately test in-house, proofs of concept at low cost
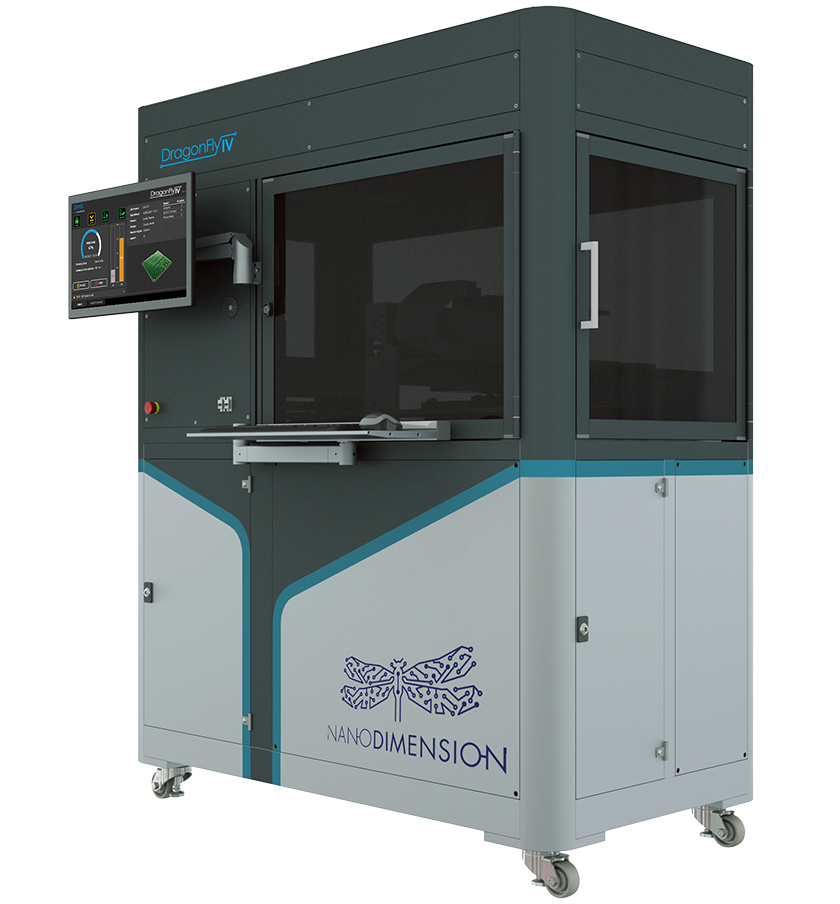