Dragonfly® IV+ Materials Datasheet
The DragonFly® IV+ system can print Conductive Ink (CI) and Dielectric Ink 1092 (DI) simultaneously to enable the production of Additively Manufactured Electronic Devices. Click to read.
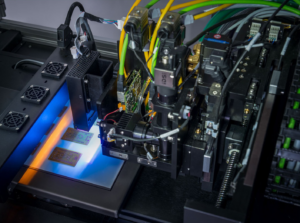
Get to know the barrier-breaking inks developed especially for the DragonFly® IV+ platform
____________________________________________________________________________________________
AgCite® Silver Conductive Ink
Our formula of silver nano-particles are optimized for sintering and curing.
Tightly Controlled Particle Sizes
Pure silver particles of 10 to 100 nanometers maintain highly predictable conductivity in traces as small as 75 μm.
Environmentally Sound
With less oxidation and less toxicity than copper, AgCite™ presents a cleaner industry alternative.
Dielectric Polymer
Our proprietary dielectric material provides both insulation and structure.
Stability and Durability
Our UV-curable acrylate ink is ready for application in a wide range of industries.
High Resolution
Allows the creation of 3D printed Electronic Devices with 18µm resolution.
Unique Compatibility
Together these advanced formulas solve the biggest obstacles to print complex circuit boards with speed and precision.
Concurrent Deposition
Both dielectric and conductive inks are simultaneously printed and cured using infrared (IR) and ultraviolet (UV) systems.
Little to No Material Waste
In contrast to traditional PCBs, the inks for DragonFly generate negligible waste and are recyclable.
Successful reliability performance based on IPC-650
· HATS (Highly Accelerated Thermal Shock) over 500 thermal cycles in the range of 0 to 100°C
_