1-MICRON
1
µ
precision opens up new vistas in miniturization
FASTER
80
%
production of micro devices compared to traditional methods
ITERATE IN-HOUSE
MOQ =
1
With ROI in the first few months
Reinvent medical devices in your lab
Groundbreaking technology that provides researchers the freedom to instantly create and innovate
Nano Dimension’s DragonFly prints fully functional 3D electronic circuitry in-house.
Researchers can also explore free-form printing of metals and dielectric polymers for entirely new applications.
Unprecedented Form Factors
Multiply layers and freely form connections inside 3D electronic devices
High
High
Performance
Fabricate embedded antennas, coils and other high-performance passive components
Short
Development
Cycles
Immediately test in-house, proofs of concept at low cost
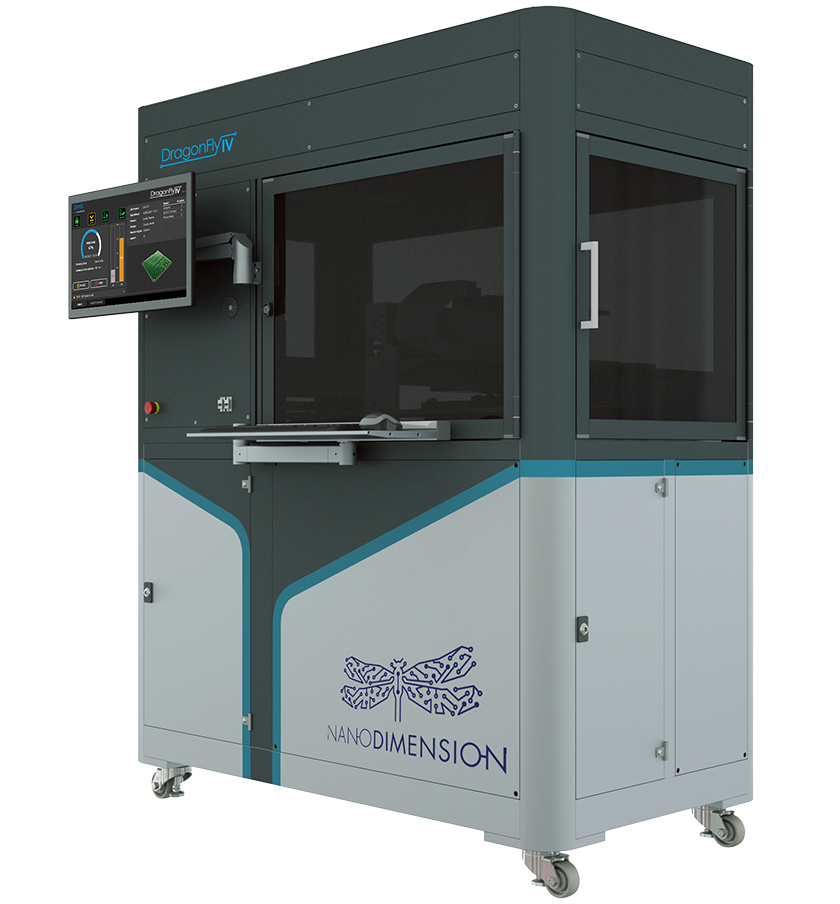